Create a World Class Organization
Six Sigma
​Overview
Six Sigma is a business management strategy, originally developed by Motorola in 1986.
It became famous post Jack Welch making it a central focus of his business strategy at General Electric in 1995, and today it is widely used in many sectors of industry.
It seeks to improve the quality of process outputs by identifying and removing the causes of defects (errors) and minimizing variability in manufacturing and business processes. It uses a set of quality management methods, including statistical methods, and creates a special infrastructure of people within the organization ("Black Belts", "Green Belts", etc.) who are experts in these methods. Each Six Sigma project carried out within an organization follows a defined sequence of steps and has quantified financial targets (cost reduction and/or profit increase).
The term Six Sigma originated from terminology associated with manufacturing, specifically terms associated with statistical modeling of manufacturing processes. The maturity of a manufacturing process can be described by a sigma rating indicating its yield or the percentage of defect-free products it creates. A six sigma process is one in which 99.99966% of the products manufactured are statistically expected to be free of defects (3.4 defects per million). Motorola set a goal of "six sigma" for all of its manufacturing operations, and this goal became a byword for the management and engineering practices used to achieve it.
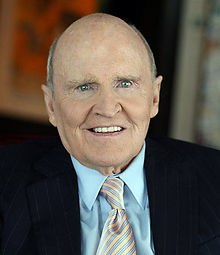
Jack Welch
​History
CEO Bob Galvin was always focused on improving the quality of Motorola products. Galvin found an ally in John F. Mitchell, a young engineer on the rise to becoming Chief Engineer. Mitchell was seen as a demanding, hands-on manager who cared for his co-workers and insisted on team effort. Mitchell believed in building quality into the engineering and manufacturing processes as a way of lowering costs and improving yield. He also favored competition among product lines and distributors as a business discipline to both reduce costs and to promote quality improvement. Mitchell’s early successes with quality control appeared with the introduction of a new digital transistorized Pager, and the formalization of improvised Mitchell Quality Tests. Mitchell also used Shainin Methods and other tests] in his operations. John F. Mitchell set the bar high for his engineers knowing they would respond. By the early 1970s, as John F. Mitchell was on his ascendancy to General Manager, Communications Division in 1972, Motorola had established itself as second largest producer of electronic equipment behind IBM, and as the world leader in wireless communication products, and had been battling Intel and Texas Instruments for the number one slot in Semiconductor sales. Motorola was also the largest supplier of certain parts and products to Japan's National Telegraph & Telephone Company, but at the same time, the Japanese were beginning to erode Motorola's lead in the Pager market. The rapid successes and expansion of the Motorola Pager business created by John F. Mitchell, as cited above, led to competitive deficiencies in quality controls, notwithstanding the "Mitchell Testing." In the late 1970s, as John F. Mitchell was on the ascendancy to being named President & COO in 1980, he was joined by other senior managers, notably, CEO Bob Galvin, Jack Germain, and Art Sundry, who worked in John F. Mitchell's Pager organization to set the quality bar 10x higher. Sundry was reputed to have shouted "Our Quality Stinks"at an organizational meeting attended by Galvin, John F. Mitchell and other Senior Executives; and Sundry got to keep his job. But most importantly, the breakthroughs occurred when it was recognized that intensified focus and improved measurements, data collection, and more disciplined statistical approaches John F. Mitchell's untiring efforts, and support from Motorola engineers and senior management, prevailed and brought Japanese quality control methods back to the USA, and resulted in a significant and permanent change in culture at Motorola. "We ought to be better than we are," said Germain, director of Quality Improvement. The culmination of Motorola quality engineering efforts occurred in 1986, with the help of an outside quality control consultant who joined Motorola, Bill Smith when the Motorola University and Six-Sigma Institute was founded. Two years later, in 1988, Motorola received the coveted Malcolm Baldrige National Quality Award which is given by the United States Congress. Later, the Six Sigma processes subsequently were adopted at the General Electric Corporation. Jack Welch said: "Six Sigma changed the DNA of GE." The Six Sigma process requires 99.99967% error free processes and products, (or 3.4 parts per million defects or less). Without the Six Sigma process controls, it may not have been possible for John F. Mitchell to launch the Iridium Constellation, one of the most complex projects undertaken by a private company, which involved some 25,000 electronic components and took 11 years to develop and implement at a cost of $5 Billion. Six Sigma processes resulted in $16-17 Billion in savings to Motorola as of 2006. A search of Safari Books Online reveals 1062 books written about Six Sigma. with 532 published since 2009